Methods of laboratory of strength and plasticity
The implementation of large plastic deformations (including cryogenic conditions)by methods of quasihydroextrusion, rolling, drawing and their combination
Creation in metals and alloys of nanometer-scale structures
![]() Dependence of the average cell size on the degree of deformation by rolling at various temperatures: |
![]() Cell size distribution in Zr, strained by rolling at 300 K (e = 3,9) |
Characteristics of nanostructured samples Zr and Zr1Nb
Material | D,nm | Nd, cm2 Dislocation density |
Cv 102Volume density of boundaries |
Zr | 82 | 3.4x1010 | 4.3 |
ZrlNb | 61 | 1.5x1011 | 3.4 |
Effects of Hardening
Additional hardening of austenitic steel at a different strain epures
Additional hardening austenitic steel as a result of combined deformation under cryogenic conditions ![]() Microhardness of 18Cr10NiTi steel on the degree deformation by drawing at 77 K (1), |
Increase the strength characteristics of austenitic steel as a result of large cryogenic deformation by quasihydroextrusion ![]() Yield strength steel 18Cr10NiTi vs strain by quasihydroextrusion at 300 K (1), 77 K (2) K and 20.4 K (3). |
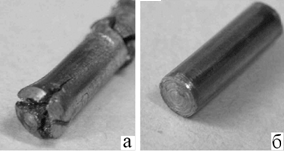
St50 steel samples strained by cryogenic quasihydroextrusion without back pressure (a) and using the back pressure (b).

Microstructure (a) and electron diffraction pattern (b) of steel 18Cr10NiTi after quasihydroextrusion at 77 K by 45% and subsequent annealing at 750 K.
Mechanical testing in tension and compression at temperature range 4,2….1000 к
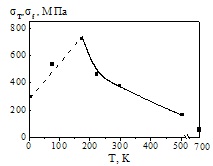
Chromium embrittlement at low temperatures.
Temperature dependences of the yield stress σТ and strain of brittle fracture σf (dashed line) the single-crystal chromium of orientation.
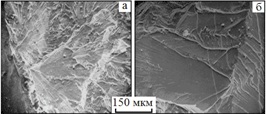
The microstructure of the fracture surface of alloy Cr-V (a) and a single crystal of Cr (b) in the ductile-brittle transition region.
The magnetic and ultrasonic treatment of constructional and functional materials
Relaxation effects in structural materials resulting magnetic and ultrasonic exposures
Increase of impact toughness and a decrease of temperature ductile-brittle transition for weld joint vessel steel as a result of exposure alternating magnetic field ![]() Temperature dependences of impact toughness of steel 15Kh2NMFA (1), weld joint before magnetic treatment (2), and after treatment (3). |
Increase of impact toughness vessel steel 15Kh2NMFA as a result of ultrasonic treatment ![]() Temperature dependence of impact toughness of the steel in the initial state (1) and after ultrasonic treatment (2). |
Change in the microhardness of nanostructured alloy Zr-2.5Nb due to ultrasonic treatment ![]() Нμ vs τ for σus=200 MPa (1) and σus=85 MPa (2). |
Relaxation effects in functional materials due to ultrasonic treatment
Enhance of mechanical stability of metal-oxide compound YBaCuO ![]() Dependence of the yield strength on the us treatment duration: 1 - ТUS = 373 К; 2 - ТUS = 573 К. |
Enhance of critical currents of technical superconductors ![]() Field dependences of the critical current density of multi filamentary (n = 55) superconducting wire based on Nb3Sn: the initial state (1), |
Creep in the temperature range 4,2…..700 К
Structural instability and effects of magnetic treatment in changing the creep rate of the irradiated vessel steel ![]() Dependences of the creep rate at T = 600 K from stress for vessel steel: |
Influence of mechanical-thermal treatment on the creep of zirconium ![]() Dependences of the creep rate at T = 300 K (1,2,3) and 700 K (4,5,6) from stress for zirconium: |
Fatigue in the temperature range 4,2…..400 К
Effect of test temperature on the low-amplitude fatigue of Zr and alloy Zr1Nb ![]() Fatigue curves of alloy Zr1Nb (1, 2) and Zr (3,4) at 293 K (1,3) and 77 K (2,4) |
![]() The structure of the surface near the place of the specimen fracture from the alloy Zr1Nb after fatigue tests at 293 K with a stress amplitude σа = 500 MPa |
Measurement of low-frequency internal friction and elastic modules in the temperature range of 4,2…..1000 К
Decomposition into the peaks of experimental curves of internal friction ultrafine-grained (UFG) titanium alloy VT6 strained by rolling at 77 K ![]() Temperature dependence of the damping decrement. |
Decrease in shear modulus of the titanium alloy VT6 as a result of cryogenic (77 K) deformation ![]() Temperature dependences of the shear modulus: |
Measurement of electrical resistivity in the temperature range 4,2….700 К and calculations of microscopic parameters of metals. metallography and transmission microscopy
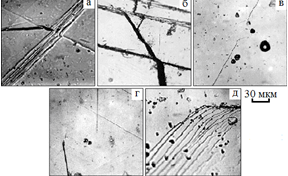
Microstructure of strained chromium single crystal.
Crack nucleation at the intersection of twins (a);
stop of a crack at twin boundary (b);
and at encounter with the other crack (c);
stress relaxation in the crack mouth by twinning (d);
and sleep (e).
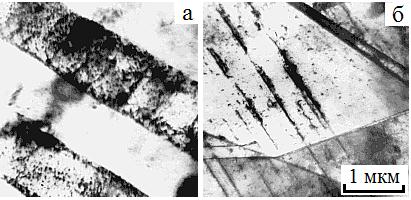
Twins (a) and microtwins (b)in zirconium strained at 4.2 K
The effective microscopic characteristics of Nb and Ta in different structural states which was calculated using the parameters of temperature dependence of electrical resistivity:
λ - electron-phonon coupling constant;
Ωр – plasma frequency,
VF – Fermi velocity,
N(0) – the density of states,
z – reduced frequency of collisions
Material | α | Ω p, eV | VF, 108cm/s | N(0), state/eV∙atom | z |
Pure Nb | 1,148 | 9,32 | 0,663 | 1,357 | 0,204 |
Nb with impurities | 1,133 | 9,83 | 0,728 | 1,237 | 1,127 |
Deformed Nb | 1,181 | 8,65 | 0,588 | 1,533 | 1,404 |
Pure Nf | 0,817 | 8,12 | 0,611 | 1,216 | 0,064 |
Ta with impurities | 0,804 | 8,16 | 0,627 | 1,191 | 1,183 |
Measurement of critical parameters of superconductors in different structural states
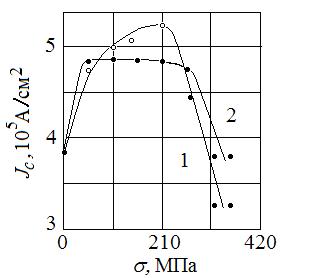
Critical currents of technical superconductors based on Nb3Sn under tensile loads.
Jс changes of multifilamentary (n = 7225) wire composite under strain (1) and in the unloaded condition (2)
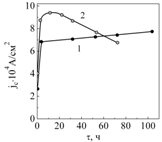
Change in the critical currents of the superconductor Nb-Tias a result of annealing at 670 K.
Jc (H=5 T, T=4.2 K) vs Τ for Nb-Ti samples strained by drawing at 300 (1) and 77 K (2).
Correlation of critical current density and normal current component for monatomic type II superconductors
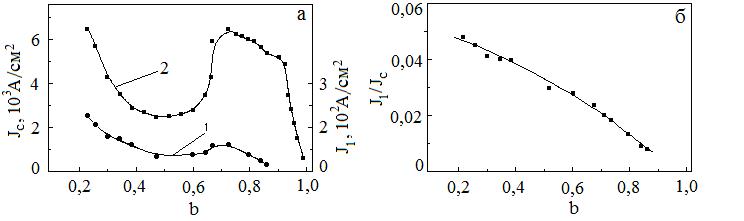
Dependences corresponding to viscous flow of the vortex lattice for Nb with a high (~1011cm-2) density dislocations:
а – normal component of current J1 (1) and critical current Jc (2) vs reduced induction;
b - б J1/Jc vs b.