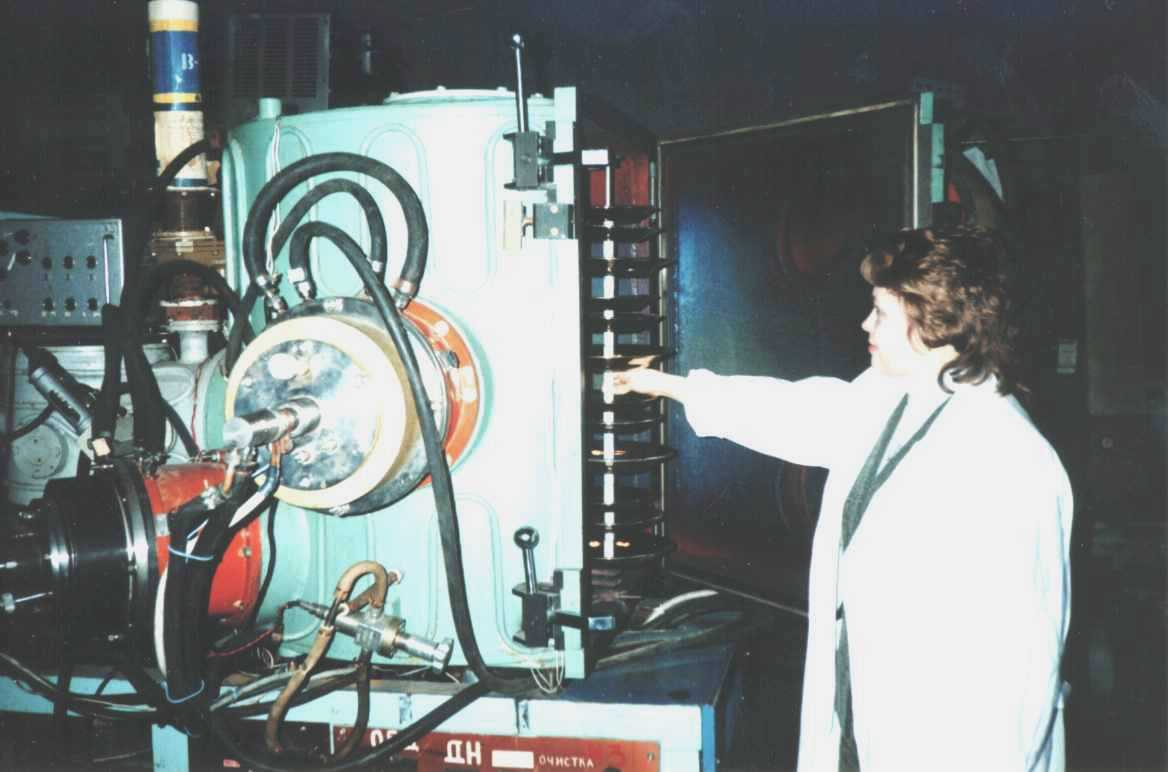
Modification of the surface of structural materials
Modification of the surface of structural and fuel materials means the change of their surface and bulk characteristics as the result of the influence of different particles flows (neutral ions, electrons) on the surface. Controlling the energy of bombarding particles we can realize the processes of surface cleaning, implantation of particles into near surface layers, deposition of coating different by composition, structure, properties and characteristics.
Activity for development of methods of coating deposition is in progress in NSC KIPT more than 30 years. Our specialists perform investigations and development for production of industrial methods, equipment and technology of coating deposition for different purposes with the use of methods:
Main lines of investigations:
- anticorrosion and antierosion protection of structural materials operating in different conditions including high temperatures (up to 2000oC);
- increasing of the service life and quality of treatment of form producing and cutting instrument;
- production of antifriction coatings on structural materials;
- formation of products by material deposition of plasma or gaseous phase;
- production of protective-decorative, bactericide and bleaching coatings;
- production of materials of new class (including nanostructural) as films with unique characteristics and properties;
- production of coatings inside the holes and tubes (up to d≤1 mm) with L>>d.
Modification of the surface of structural materials is based on following methods:
- Vacuum-arc ion-plasma deposition of coating
- For generation of plasma flux heavy current vacuum-arc discharges are used. Control of parameters and composition of plasma provides the realization of ion-plasma cleaning, formation of transient zones base-coating, deposition of composite coatings (oxides, nitrides, carbo-nitrides etc) and also allows to realize the ion implantation under energies up to tens of KeV;
- Gaseous-phase and plasma-chemical processes
- They provide the deposition of protective coatings of refractory metals on different articles including capillary tubes and production of pieces of molybdenum, tungsten silicon.
- Activated thermal diffusion saturation in vacuum
- These methods allow the deposition of protective coatings on different structural units (including molybdenum, tungsten, carbon, providing long-term operation of articles in air at temperatures up to 2000°C.
Specialists of the institute are explorers and leaders in the fields:
- production of industrial technologies and equipment for deposition of functional coatings by developed methods;
- synthesis of diamond-like films from vacuum arc burning in carbon vapors;
- synthesis of polycrystalline diamond layers and coating of different purposes from carbon-containing gaseous mixtures;
- development of plasma optical systems for separation of metallic plasma;
- production of extended systems of metallic plasma generation;
- development of equipment and of processes for production of thick (of the order of millimeter) coatings and pieces by vacuum-arc or plasma-gaseous methods;
- Development and realization of equipment and technologies for ion-plasma modification Of the surface of nuclear structural materials;
- development of processes and of equipment for plasma-chemical reduction of metals, halogens and oxides.
In our institute you can obtain directly from development engineers unique techniques and sets, produced for solution of yours problems, qualified recommendations and advises for utilization.
International cooperation
Department develops, supplies equipment and units to international companies.
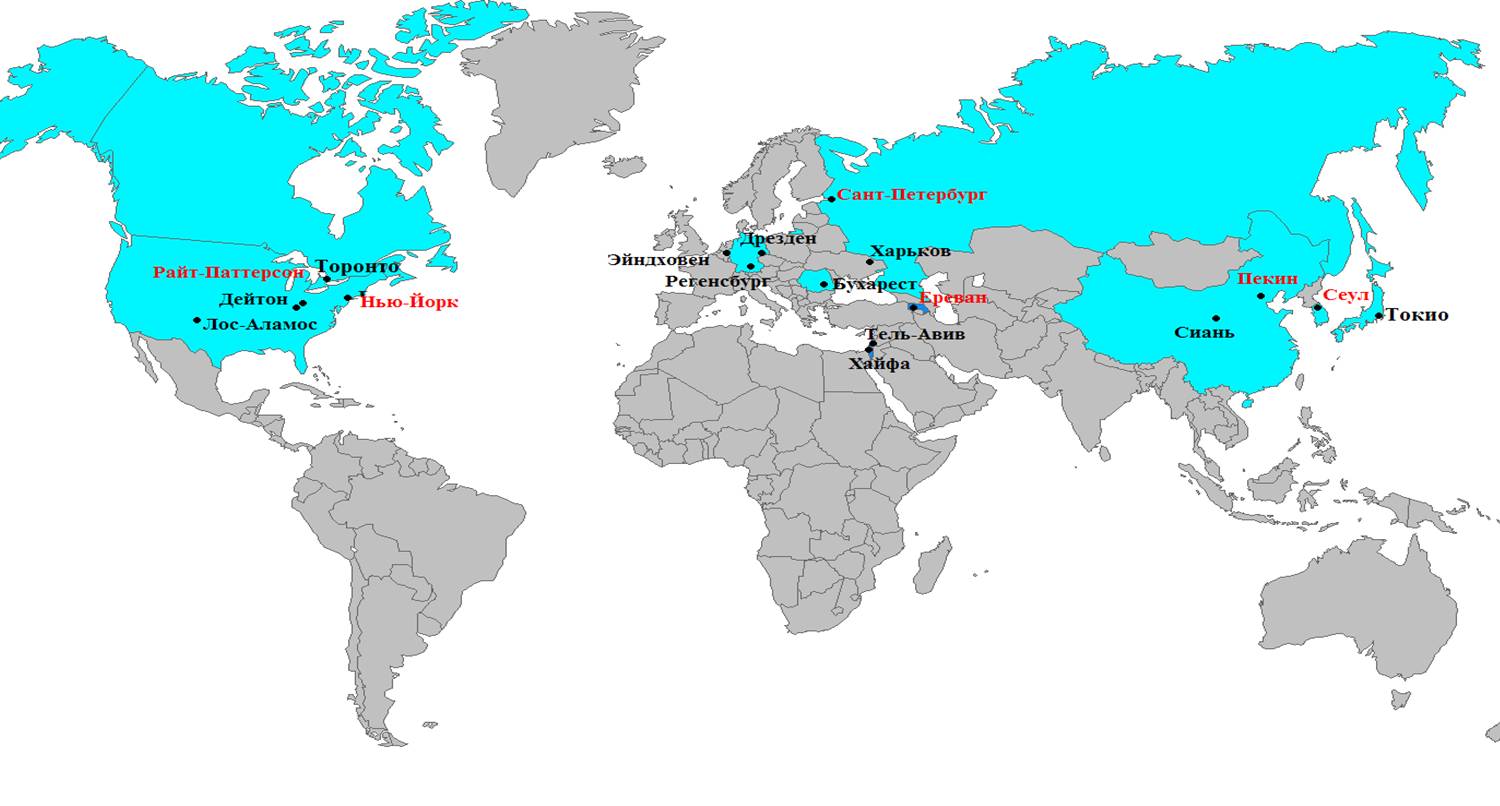