Высокопроизводительные методы осаждения покрытий. Метод АИР
Назначение - напыление нано- и микрокристаллических металлических, металл-металлоидных и керамических покрытий толщиной от 0,001 до 1 мм на лопатки турбин, детали машин, режущий инструмент, сопла двигателей малой тяги.
Основные области применения - реакторные материалы, авиационное и ракетное двигателестроение, нефтехимическое и нефтеперерабатывающее оборудование, машиностроение, медицинский инструмент, автомобилестроение
Базовая промышленная установка АИР-3
![]() АИР-3 с дуговой |
![]() АИР-ЗМ с ВЧ ионизацией паровой фазы |
Базовая промышленная установка АИР-3 содержит электронно-лучевой испаритель с ионизатором, плазменный источник ионов инертного газа и электродуговой испаритель, аналогичный испарителям в установках типа Булат-6. В СССР к 1990 г. было изготовлено 10 установок. Размеры камеры: диаметр-1м., высота-0,75м.
Особенность и достоинство установок АИР
- применение двух независимых источников металлической плазмы;
- наличие мощного источника газовой плазмы;
- возможность установки электронно-лучевого модуля с сепарацией плазменного потока от микрокапель;
- pеализация высокопроизводительных экологически чистых технологий.
Технические характеристики АИР-3
Максимальная мощность потребления электроэнергии, квт, не более | 60 |
Напряжение питания (3-х фазное), В | 380/220 |
Электродуговой источник металлической плазмы, шт | 1 |
Источник газовой плазмы, шт | 1 |
Электронно-лучевой испаритель(30квт), шт | 1 |
Сепаратор плазмы | 1 |
Система откачки: ▪ электродуговой насос (8000л/с) ▪ диффузионный насос (500л/с) ▪ форвакуумный насос (60л/с) |
1 2 3 |
Расход воды, м3/час | 4 |
Рабочая камера, мм Диаметр Высота |
1000 750 |
Полезный объем камеры, мм Диаметр Высота |
700 500 |
Скорость осаждения на плоскость на расстоянии 0,5м мкм/час | 70-200 |
Допускаемая нагрузка на шпиндель подложки, кГс | 50 |
Новые технологические процессы и оборудование для высокоскоростного нанесения ионно-плазменных покрытий методом атомно-ионного распыления (АИР).
Метод атомно-ионного распыления (метод АИР - оригинальное авторское название создателей метода) - это физический метод нанесения покрытий (толстых плёнок) в вакууме, путём электронно-лучевого испарения материала, ионизации паров испаряемого материала электродуговым сильноточным несамостоятельным разрядом (или ВЧ разрядом) и конденсации атомно-ионных потоков на подложку (изделие, деталь).
Начало работ по созданию и первым промышленным применениям метода, которые инициировались одним из крупных заказов Министерства среднего машиностроения СССР (февраль 1978г.), касающимся антикоррозионной защиты урановых материалов.
В выполнении этих работ принимал участие один из научных коллективов Харьковского физико-технического института (сейчас ННЦ ХФТИ) под руководством заместителя директора Зеленского В.Ф.. Участниками разработок были: Картмазов Г.Н., Павлов В.С., Белоус В.А., Сафонов В.И., Слепцов С.Н., Расторгуев В.П. и др.
Метод сочетает в себе достоинства электронно-лучевого и ионно-плазменного методов нанесения покрытий - высокие производительность (скорости нанесения покрытий достигают ∼0,1-1мкм/с) и степень ионизации потоков пара (10…70%).
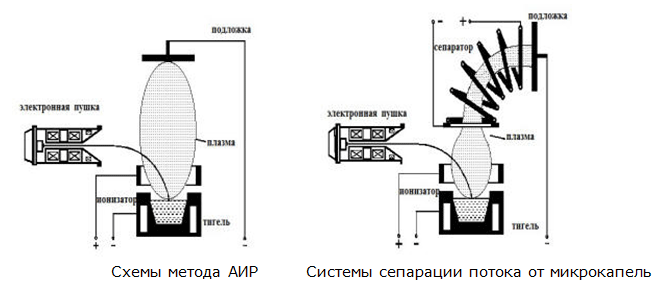
Разработаны системы полной очистки плазмы от микрокапель и нейтральных частиц с высокими показателями прохождения плазмы через сепаратор (до 50%). Распыляемыми материалами могут служить как металлы, так и их соединения в виде окислов, карбидов и др.
Покрытия в виде соединений могут также формироваться при распылении только металлов, если осаждение производится в среде того или иного активного газа или смеси газов (аналогично возможностям других ионно-плазменных методов).
Способ ионизации дуговым разрядом обусловливает однозарядность и небольшую начальную энергию ионов (5…7 эВ), что обеспечивает формирование практически моноэнергетического потока электрически ускоренных ионов. Это обстоятельство позволило с успехом провести численное математическое моделирование процессов осаждения многокомпонентных покрытий, создать физическую модель ионного уплотнения нарастающих конденсатов, разработать физические основы ряда технологических процессов. Этими исследованиями внесен существенный вклад в формирование одного из новых направлений физики твердого тела - ионной металлургии.
В рамках этого направления созданы новые материалы с уникальными свойствами, в т.ч. на базе разработанных неравновесных диаграмм состояния систем металл-металлоид. Такие диаграммы характеризуются наличием метастабильных соединений, сверхпересыщенных твердых растворов с предельной растворимостью, превышающей равновесные значения в 103…104 раз; структур аморфного и нанокристаллического типа при температурах конденсации до 900 К и др.
Атомно-ионное распыление позволяет получать за короткое время (несколько часов) толстые ионно-плазменные покрытия (1…2 мм) и самонесущие массивные изделия (методом наращивания слоев на подложке) с особыми свойствами. Величина достигаемого технологического эффекта в таких покрытиях и изделиях часто превышает 10-кратное увеличение эксплуатационных параметров обычных материалов.
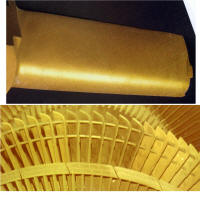
Разработки защищены рядом авторских свидетельств СССР на изобретения и патентами, в т.ч.: Авт. свид. СССР. С 23 С 14/00. Способ нанесения покрытий в вакууме/ Белоус В.А., Картмазов Г.Н., Сафонов В.И. и др. Открытия. Изобретения. 1986. №40. Авт. свид. преобразовано в Патент Украины № 47545, 15.07.2002. Бюл. №7
Наши возможности
Tехнологические, исследовательские.
Возможные области промышленного (практического) применения:
- испарение керамики, чистых металлов и сплавов;
- восстановление изношенных поверхностей;
- получение тонкостенных самонесущих изделий;
- замена гальванических процессов;
- размер покрываемого изделия (цилиндр) - диаметр 350 мм, длина до 600 мм, максимальная скорость осаждения 0,1 - 1мм/час.
Сотрудничество
- совместная разработка новых технологий и их последующая реализация;
- организация совместных предприятий по созданию и выпуску новых моделей установок АИР;
- заключение договоров на разработку технологических процессов нанесения защитных покрытий на изделия сложной геометрической формы (лопатки турбин, детали машин, режущий инструмент, узлы прессов и др.).